Interview with the experts
- Salmonella
Salmonella, a prevalent foodborne pathogen worldwide, encompasses over 2500 distinct serovars. Among these, Enteritidis and Typhimurium stand out as the most common culprits in human infections. This ubiquitous organism infiltrates the feed-food chain through various vectors. To maintain safety standards, rigorous Salmonella control measures must be implemented at every stage of the production chain. These measures require continuous verification and optimization. Internally, the food production industry faces additional challenges due to antimicrobial resistance
Below, our Salmonella experts are answering questions addressing to effective salmonella control strategies.
About our experts
Pieter Steyn
Pieter has been in the agricultural industry for over 10 years, including spending 3 years at a local Feed Additive company in South Africa. Pieter's focus has always been related to feed safety in feed mills which included raw material preservation as well as Salmonella control in final feed. Pieter was born and raised in South Africa, where he attained his education at UNISA in Marketing Management.
Marcos Rostagno
A veterinarian, holds both an M.Sc. and a Ph.D. in Preventive Veterinary Medicine. His professional focus lies in Salmonella ecology, epidemiology, antimicrobial resistance, and gut health in poultry and swine. With extensive academic and industry experience, he currently serves as the U.S. Technical and Innovation Director at Selko-USA.
FAQ with Pieter and Marcos
Its important to know the serotypes since some serotypes are not responding to some interventions.
Marcos: I agree, but serotyping does carry a higher cost, as well as requires more time and labor. Plus, finding the same serotype in different samples or stages along the production chain does not guarantee that the isolates are exactly the same strain or represent the same clone. There are molecular typing techniques that are far more precise than serotyping. However, they also add more cost to the program.
The goal of the program should determine the sampling program as well as the level of refinement in the identification of the Salmonella found. The observation that some serotypes are not responding to some interventions can be true, but at the same time, misleading. If failure of an intervention is suspected, further evaluation of the program and the intervention itself should be carried out by experts. Simply changing the intervention (or other things in the program) without knowing what is going on can lead to a lot of additional cost and frustration.
What is the best and most accurate method to test Salmonella contamination in raw materials?
Marcos: I would suggest a very well-planned sampling program, in combination with a detection method with high sensitivity. It will likely be expensive in the beginning, but as the program evolves it can and should be adjusted accordingly. Salmonella sampling and monitoring programs are not static and require continuous evaluation and adjustment, based on improved understanding of the sources and frequency of the contamination.
Pieter: In addition to what Marcos mentioned you will see certain times of the year might be higher risks than others. This is also a reason why you constantly need to adjust and measure and make continuous improvements to your sampling plan.
What kind of microbiological analysis do you do to monitor Salmonella throughout the chain?
Pieter: We do a range of microbiological analysis that includes moulds/yeasts, enterobacteria and Salmonella. Enterobacteria is a very good indicator of the current risk faced in a particular raw material. When we look at cfu/g, anything above 10000 cfu/g would be alarming and we would test for Salmonella.
Marcos: There are different options that can be used according to the strategy of the program, as their performance (sensitivity and specificity) and cost are variable. Detection methods are usually faster to generate results (eg., ELISA, PCR, and others), whereas bacterial culture/isolation usually takes longer to complete. If faster turnaround time and no further analysis is intended, detection methods should suffice. However, if there is interest in identifying specific strains, serotypes or even antimicrobial resistance profiles, then bacterial culture/isolation is needed. In summary, the goal of the program will determine what method should be used. However, in some cases, combinations are applied, but at a higher cost.
How quickly can you get results from the laboratories?
Marcos: It depends on the bacteriological method used. If rapid detection methods are used, a 24-48h turnaround is possible, whereas if culture/isolation is used, then at least 4-5 days will be required. If typing of the isolates recovered is intended (serotyping and/or molecular typing), additional time is usually required.
Constantly adjust, measure, and make continuous improvements to your sampling plan is important
In your critical control points, how frequently do you test each of those critical points?
Marcos: My approach is to determine how frequently neglected the CCP is in a system, and then, based on that frequency, monitor execution of its mitigation as well as increase sampling to drive execution of the applied intervention. Also, some CCPs are more important than others (keep in mind that risk is a relative to the hazard in focus), and therefore, justify more attention to it to make sure that any intervention is appropriately executed and results in the mitigation of the CCP targeted.
Pieter: And be consistent with the CCP’s you do sample and analyze to get a good trend of risks through the process. Understanding the microbial blueprint of your process enables you to act quicker in the case of contamination.
How do we effectively clean the production pipeline (eg conveyor belts, bucket elevators) in feed mills?
Pieter: Physical cleaning is always the best start in controlling the risk of contamination or recontamination. These CCP’s mentioned are normally places which are difficult to clean or that are not regularly cleaned. We, at Selko, suggest Fysal SP (dry product) and flush that through the conveyor system using raw materials as a carrier. When you use raw materials like maize that is a bit coarser, it can scrape off some build up in the conveyors and this helps with cleaning as well. Alternatively, we also use a powder duster to apply the Fysal SP in the bucket elevators.
Do you think use of organic acids blends is an effective strategy to prevent Salmonella on feed? and how do you see formaldehyde using in Brazil, still a good and safe strategy?
Marcos: Organic acids can be applied successfully to prevent/control Salmonella in the feed. It is important to highlight that there are differences between individual and combinations of organic acids, regarding their effectiveness. On the use of formaldehyde, it is well known as a powerful intervention, being very effective. The issue with using formaldehyde is the risk it poses, particularly to the safety of employees exposed to it. Formaldehyde is a well-known toxic and carcinogenic compound.
is the use of organic acids is the only fool proof method to control Salmonella?
Marcos: Unfortunately, there is no such thing as a fool proof method to control Salmonella, due to the many variables involved and briefly discussed in our presentation. In vitro or under controlled conditions, most interventions show great effectiveness. However, the same results are frequently not achieved under commercial or field conditions, due to a variety of factors. Organic acids do constitute great intervention tools, but their probability of success will significantly increase when applied as part of a broader control program, in combination with other interventions. Use of organic acids do carry several positive points, such as effectiveness, convenience, flexibility, and competitive cost. However, like any intervention, they need to be applied correctly.
Pieter: There are so many factors playing a role like Marcos mentioned so it is not a one magic product approach, it is really controlling the whole process. From when the trucks are offloading your raw materials straight through the process when it comes to the heating step and then making sure we take care of the risk of recontamination. Cleaning remains the number 1 starting point especially in a production process.
In controlling Salmonella, prevention is always better than treatment
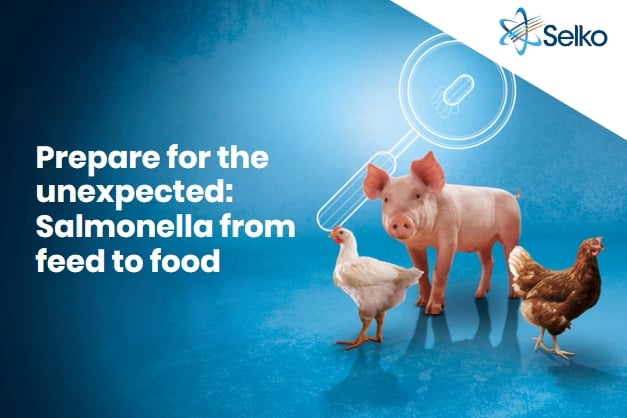
Did you miss our webinar on Salmonella? It's not too late to catch up and learn from our industry experts. In June, we hosted an insightful webinar on Salmonella control, featuring two industry experts above.