Raw Material Quality Programme
Raw material quality is paramount for safe feed and food production. Grains like corn, wheat, and barley face challenges in the field, susceptible to mould, mycotoxins, and harmful bacteria due to environmental factors. In addition to that, oilseeds like soy, canola, and sunflower, processed into high-protein meals, pose microbial risks. Rigorous quality control measures are essential, involving advanced agricultural practices, proper storage, and continuous monitoring. Implementing comprehensive strategies ensures product safety, upholding the integrity of the food and feed supply chain.
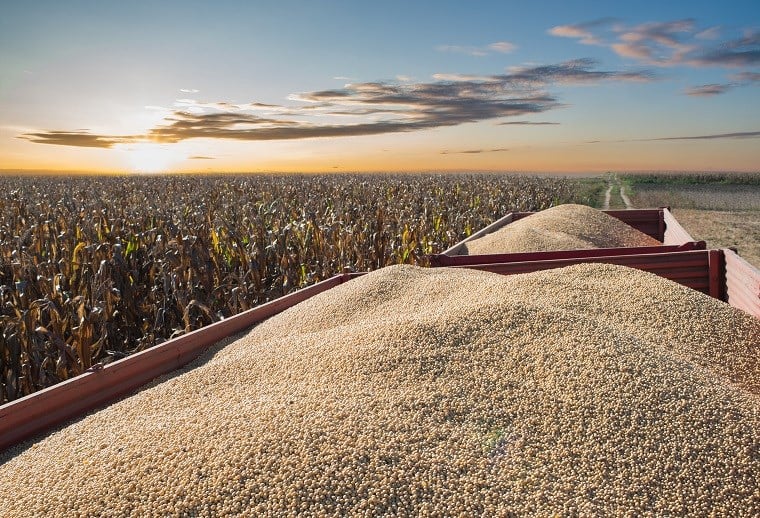
The programme aims to build strong partnerships within the grain industry, in a shared effort to provide safe feed materials, and comprises:
- The sharing of in-depth knowledge about grain and oilseed hygiene, best practices for storage and processing, and effective product application.
- Thorough plant hygiene scans that identify critical control points, analyse samples, and propose the best possible treatments.
- A strong portfolio of potent blends of validated and assessed organic acids, with proven efficacy in commercial circumstances.
- State-of-the-art dosing equipment that allows for safe, accurate dosing of treatment products and optimal dispersion and absorption.
- Continuous monitoring and reporting on progress and adaptation of the programme where needed. This can be in the form of decontamination or shift to the prevention of microbial risk as the programme evolves within your plant.
Implementing the programme for grains and cereals
Grain storage techniques
When it comes to grains and cereals, moulds that generate mycotoxins are a constant concern. About 80% of agricultural commodities are infected with mycotoxins, which can make them unsuitable to be used in feed. Moulds can be hosted in damaged kernels or broken grains and can impact grain quality, both in the field and during transport and storage. Only considering reductions in stored grain, losses during storage as well as mycotoxin contamination can be more than 30%.
Contamination prevention against the adverse effect of moulds should start in the field and continue through transport, storage and production. Scoring systems created by the USDA for corn and other grains are a helpful tool for evaluating quality factors, including grade, moisture, nutritional profile, physical quality and mycotoxin presence.
Grain storage requires careful planning, management and monitoring to prevent spoilage, maintain grain quality and ensure profitability. We defined eight main points that are important for ensuring a well-maintained storage facility:
1. Grain moisture control
Moisture is another critical factor in grain storage. Too much moisture can lead to mould growth, and spoilage, while too little moisture can result in drying out and loss of weight. Maintaining appropriate moisture levels in grain storage facilities requires proper grain aeration, temperature control, and moisture monitoring to prevent spoilage and ensure grain quality.
2. Storage temperature
Temperature control is crucial in grain storage to prevent grain spoilage and insect activity. If grains are stored in conditions that are too warm, it can accelerate the growth of insects and microorganisms, leading to spoilage. Conversely, if grains are stored in conditions that are too cold, it can result in condensation and mould growth. Proper insulation, ventilation, and temperature monitoring are essential to maintain the right temperature for grain storage.
3. Grain quality control
Grain quality is critical for marketability and profitability. Factors such as moisture content, foreign material, and damaged grains can affect the quality of stored grains. Regular quality monitoring, through sample analysis helps to identify risks to allow effective grain preservation methods to be implemented.
4. Pest infestation
One of the biggest challenges in grain storage is preventing pest infestation. Insects, rodents, and other pests can damage grains, reducing their quality and market value. Controlling pests in grain storage facilities requires proper sanitation practices, regular monitoring, and the use of insecticides and rodenticides.
5. Storage capacity
Another challenge in grain storage is having enough storage capacity to accommodate the harvested grains. To properly aerate and ventilate silos, they cannot be over loaded with material. Inadequate storage capacity can result in spoilage or the need for alternative storage solutions, which may not be ideal for maintaining grain quality. Proper planning for storage capacity, including estimating grain volumes, and investing in adequate storage infrastructure, is essential to avoid storage challenges.
6. Safety and health risks
Grain storage facilities can also pose safety and health risks for workers. Hazards such as dust explosions, toxic gases, and working in confined spaces can result in accidents, injuries, or, in extreme cases, fatalities. Implementing proper safety protocols, providing adequate training to workers, and using appropriate safety equipment are essential to mitigate these risks.
7. Environmental factors
Extreme weather conditions like high humidity, floods, or storms, can impact grain storage. These factors can cause moisture increase, damage storage infrastructure, and affect grain quality. Implementing measures such as proper sealing, waterproofing, and disaster preparedness plans can help mitigate the impact of environmental factors on grain storage.
8. Regulations and compliance
Compliance with local, state, and federal regulations related to grain storage, such as environmental regulations, food safety standards, and building codes, can also be challenging. Keeping up-to-date with regulations and ensuring compliance can require additional effort, resources, and expertise.
Interview with Pieter Steyn
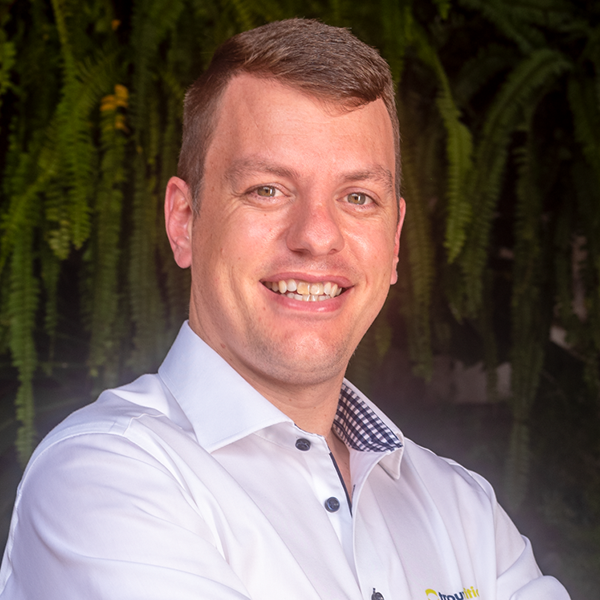
Effective grain preservation techniques
How can I best determine my preservation needs?
To create a customised and effective grain preservation plan, it is important to understand the current status of a storage location. To start, I propose that you answer the following questions:
- What are your current storage conditions, including temperature, humidity and aeration?
- What are the moisture levels, and are they within the recommended range for the specific type of grain being stored?
- Are you aware of the current microbial load in your grain bulk?
- Are there any visible signs of spoilage, such as mould growth, bad odours or discoloration in the grains?
- What is the duration of your storage?
What actions can I take to prepare the storage silos?
Before storing grains, make sure that the storage area is clean and free from any debris, dirt, insects, etc. This is particularly important when a previous batch of grain stored in the silo was contaminated. It may be necessary to fumigate the area before storing new grains.
While grains are best stored between 10ᵒ C and 15ᵒ C, realistically, this is not always possible. Nevertheless, it is important to know that temperatures above 30ᵒ C significantly increase the spoilage rate. Proper aeration and ventilation need to be in place before grains are stored.
Perhaps an obvious precaution is the importance of rotating grains, though in practice it is not always as easy as it seems, especially in flat storage facilities. Older stock needs to be used up before new grains are added.
Finally, I would always advise handling grains with care. Every time grains are handled or transported, there is a risk of damaging the outer skins, which leaves the delicate inner core unprotected against invading microbes or pests. When there is a lot of grain damage, it is advisable to treat the grains with effective organic acid solutions that also help prevent recontamination further along the feed production process.
How can microbial load and mycotoxins be reduced in the intake pit?
To determine if treatment of grains is needed, and which treatment is best, it is important to be aware of the microbial load upon receipt of the grains. This is especially important since microbes such as moulds can already negatively impact quality without being visible and can only be discovered through sample analysis.
Preservation with a synergistic blend of specific organic acids drastically reduces microbial load and helps protect against further deterioration and recontamination. This will help safeguard the nutritional value and extend the shelf life of your grains.
However, moulds that were already present in the grain could have already excreted mycotoxins. These toxins cannot be deactivated by organic acids (or even heat treatment in most cases) and need specific mycotoxin mitigation agents to prevent a negative impact on animal health and performance.
Once grains are stored, how can quality be maintained?
Once grains are stored, monitoring becomes even more important to understand their quality and its possible degradation. Constant monitoring through temperature and moisture sensors in the silos help to detect early signs of microbial development so that measures can be taken. A spike in temperature, for example, is a clear indication that you need to adjust the ventilation or aeration.
In addition to monitoring with sensors, I would recommend that you take samples at different parts of the storage area to allow for a clear picture of the grain conditions. Look for signs of spoilage, such as mould growth, discolouration, a musty smell, or evidence of insect or rodent infestation. If there are clear indications of microbe development or pests, you may need to treat the stored grains. This is usually done by spraying the grains with organic acid blends, such as Fylax Grain, while they are on the transportation line to another storage silo.
Implementing the programme for oilseed proteins
Salmonella control in oilseed protein
Of all grains, grain-by products and other feed ingredients, high-protein oilseeds pose the highest risk of contamination with microorganisms, such as moulds, yeasts, Salmonella and other harmful bacteria. Salmonella is the main point of concern, due to the possible human health impact and regulatory restrictions in regions around the world.
In some places, including the European Union, contaminated materials cannot be sold. This causes blocked stock, disrupts the production of feed, and can lead to negative publicity for companies associated with Salmonella contamination.
Selko offers specialised harbour treatments for barges arriving with material that has tested positive for Salmonella.
Effective Salmonella control
Long, oversea, shipping means grains have to endure fluctuating temperatures and humidity. While seemingly in mint condition at the harbour of departure, the story can be completely different upon arrival.
Here's how Selko can help prevent further deterioration of grains.
Plant gap analysis
To help guarantee material and plant hygiene, it's important to know where to implement solutions in the production process. Whether you treat materials upon receipt, or treat by-products after processing, the moment of product application can make a significant difference in the occurrence and risk of microbial contamination.
Selko offers a service that helps define these critical control points. Through a plant audit and sampling with our raw material analysis kit, we analyse samples at various points within the plant to pinpoint exactly where our solutions will have the highest benefit.
Several swabs and product samples are gathered and sent to our Masterlab for qualitative analysis and to test for the presence of possibly harmful microbes. We share the results with you and together determine the best way forward.
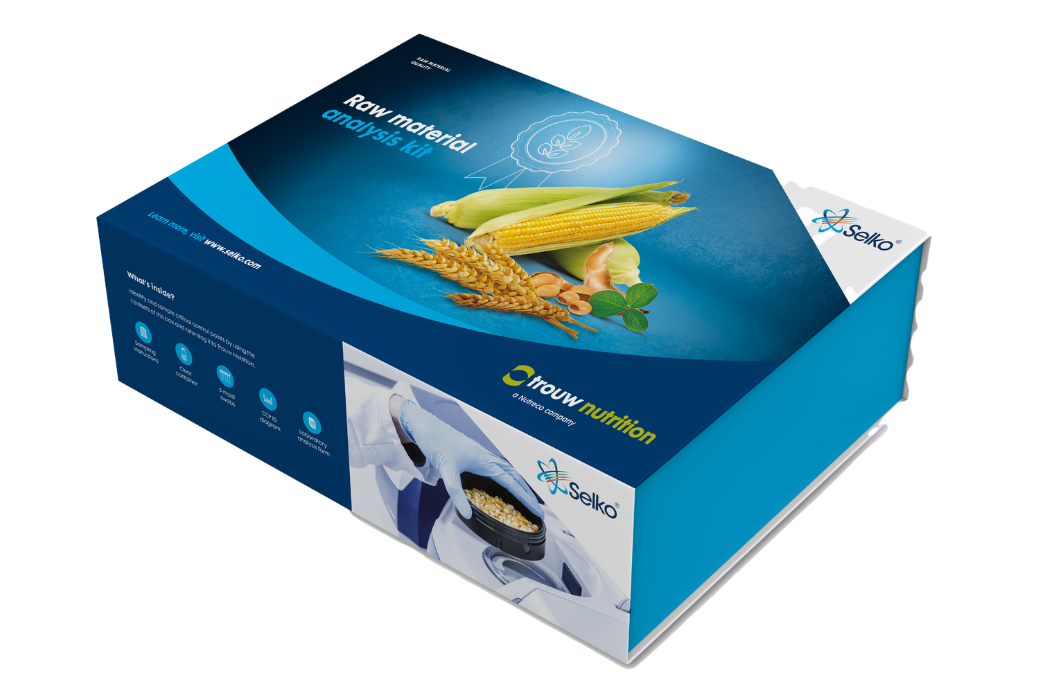
Applying effective preservation
While selecting the most appropriate product within the Selko portfolio is critical, proper and safe application is equally important. Selko has decades of experience in researching the most effective ways to treat raw materials within the feed production chain. We can help you navigate the different types of dosing equipment to allow for safe, accurate and even fully automated distribution of organic acid blends. From the type of nozzles to flow rates and pumps, our extensive research has enabled us to develop a portfolio of highly stable, accurate and easy-to-use systems.
Dosing equipment can apply Selko liquid products at any step of the production chain, depending on the needs of your facility.